Partial Discharge Detection
Prevent Electrical Insulation Failures Before They Lead to Catastrophic Damage
Understanding the Risk of Partial Discharges
Partial discharges (PD) are localized electrical discharges that occur due to insulation degradation in high-voltage equipment. Over time, these discharges can deteriorate insulation materials, leading to arc flash incidents, equipment failures, and costly unplanned downtime. If left undetected, partial discharges can cause complete insulation breakdown, resulting in catastrophic electrical failures.
Common causes of partial discharge include:
⚡ Aging or degraded insulation in switchgear, transformers, and cables
⚡ Moisture, contamination, or voids within electrical insulation
⚡ Improper installation or mechanical stress on high-voltage components
⚡ Overvoltage conditions and repeated electrical stress
Explore Our Solution Range
At Volterra Techniks, we provide state-of-the-art partial discharge detection solutions to help businesses detect, diagnose, and prevent insulation degradation before they lead to costly failures. Our technologies enable real-time thermal monitoring, ensuring proactive risk management and optimal system performance.
reduce arcing risk with no contact inspections
Ultrasound-Enabled IR Windows
Traditional partial discharge (PD) inspections often require technicians to open electrical panels, exposing them to arc flash hazards and high-voltage risks. Our IR windows with built-in ultrasonic detection provide a safe, non-intrusive way to monitor PD activity while simultaneously enabling infrared thermal inspections—all without exposing personnel to live electrical components.
By combining infrared and ultrasonic technologies, these advanced multi-functional inspection windows allow for:
✅ Real-time partial discharge detection through ultrasonic monitoring
✅ Thermal inspections without opening energized panels
✅ Reduced arc flash risk and compliance with NFPA 70E safety standards
✅ Safer and more efficient predictive maintenance programs
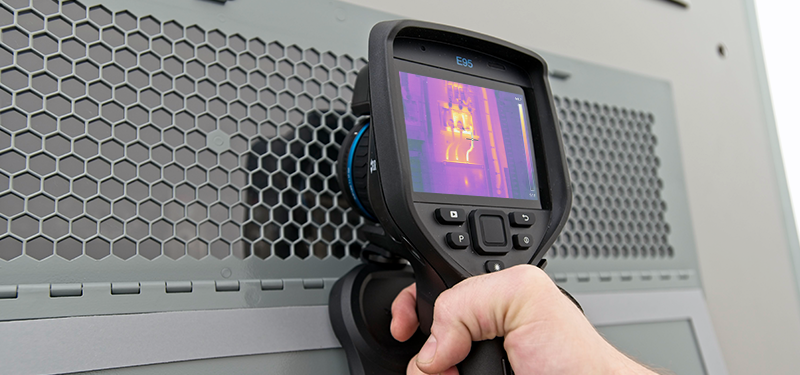
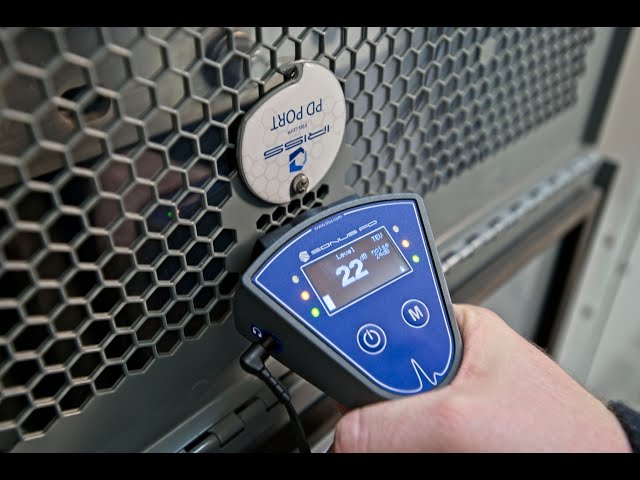
early fault detection and preventative maintenance
Ultrasound Monitors
Our ultrasound monitoring solutions deliver precision and efficiency in detecting partial discharge and other equipment anomalies before failures occur. By integrating advanced sound port technology and handheld testing devices, these monitors capture high-frequency sound waves generated by insulation faults, arcing, and mechanical wear, allowing maintenance teams to perform early diagnostics and proactive interventions.
As a key component of Condition-Based Maintenance (CBM) programs, our ultrasound monitors help industries identify defects, minimize downtime, and optimize operational efficiency. The data collected supports the development of enhanced reliability and predictive maintenance plans, ensuring greater asset longevity and improved workplace safety across critical systems.
Key Benefits of Ultrasound Monitoring:
✅ Enhanced Diagnostic Accuracy – Detect and pinpoint insulation breakdown, corona, and arcing with high-precision ultrasound sensors.
✅ Minimized Downtime – Early fault detection prevents unplanned outages and costly emergency repairs.
✅ Sustainable Maintenance Practices – Enables condition-based and predictive maintenance strategies, extending equipment lifespan and reducing waste.
Why Choose Us
Our Unique Value Proposition
Discover what sets Volterra Techniks apart and makes us the ideal choice for your industrial safety needs.
Innovation
We thrive on innovation, continually partnering with established leaders in the field to deliver unique solutions.
Expertise
Our team of seasoned professionals brings unmatched expertise to every project, ensuring quality and excellence.
Collaboration
We value collaboration, fostering partnerships and teamwork that result in groundbreaking solutions.